Cathodic Arc Deposition
High Hardness Ceramic Coatings

Cathodic Arc Deposition is a PVD technique, allowing for the formation of very thick, dense coatings.
This is due to very high deposition and ionization rates (>90%).
Pure metal or metal alloy coatings can be produced with this surface technique.
A wide variety of ceramic coatings can be produced to fit the specific requirements of a project such as max operating temperature, hardness, friction, and cost.
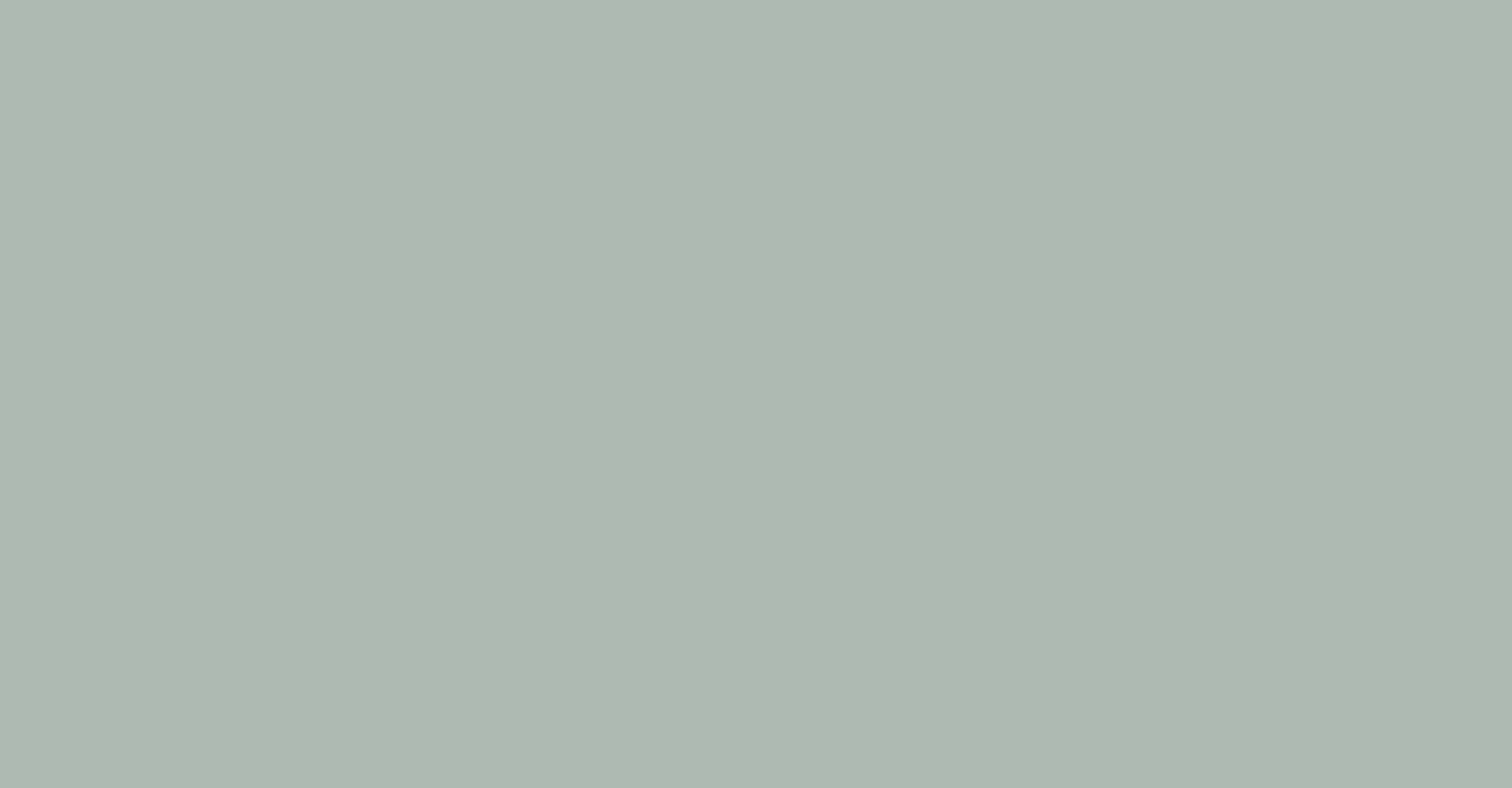
Aluminum (IVD) — Titanium —
Iron — Molybdenum — Chromium
+ Nickel — Zirconium — Nickel
Gold • Pale Gold
Silver Gray • Blue Gray • Dark Gray
Purple • Black
High-hardness ceramic coatings for increasing part-life
Surface Engineering Technologies LLC applies metal and ceramic Physical Vapor Deposition (PVD) coatings to tools and parts using a proprietary, low-temperature cathodic arc process.
Most metals can be used to apply coatings from 0.2 to 15 microns thick.
By applying coatings at temperatures below 150ºC, SET preserves the integrity of the part’s dimensions without heat-related warping. The process also preserves any existing heat treatment of aluminums and steels.
Substrate materials that can be processed include brass, bronze, titanium, aluminum, steel, glass, chrome, nickel-plated ceramic, and carbides.
Each of the coatings has a specific application, determined by cost, frictional need, operating temp, action of the wearing motion, and maximum required tool life. Molybdenum Disulphide and Heavy Metal Ion Implantation processes can be combined with these coatings to get incredibly high-performing and durable surfaces.
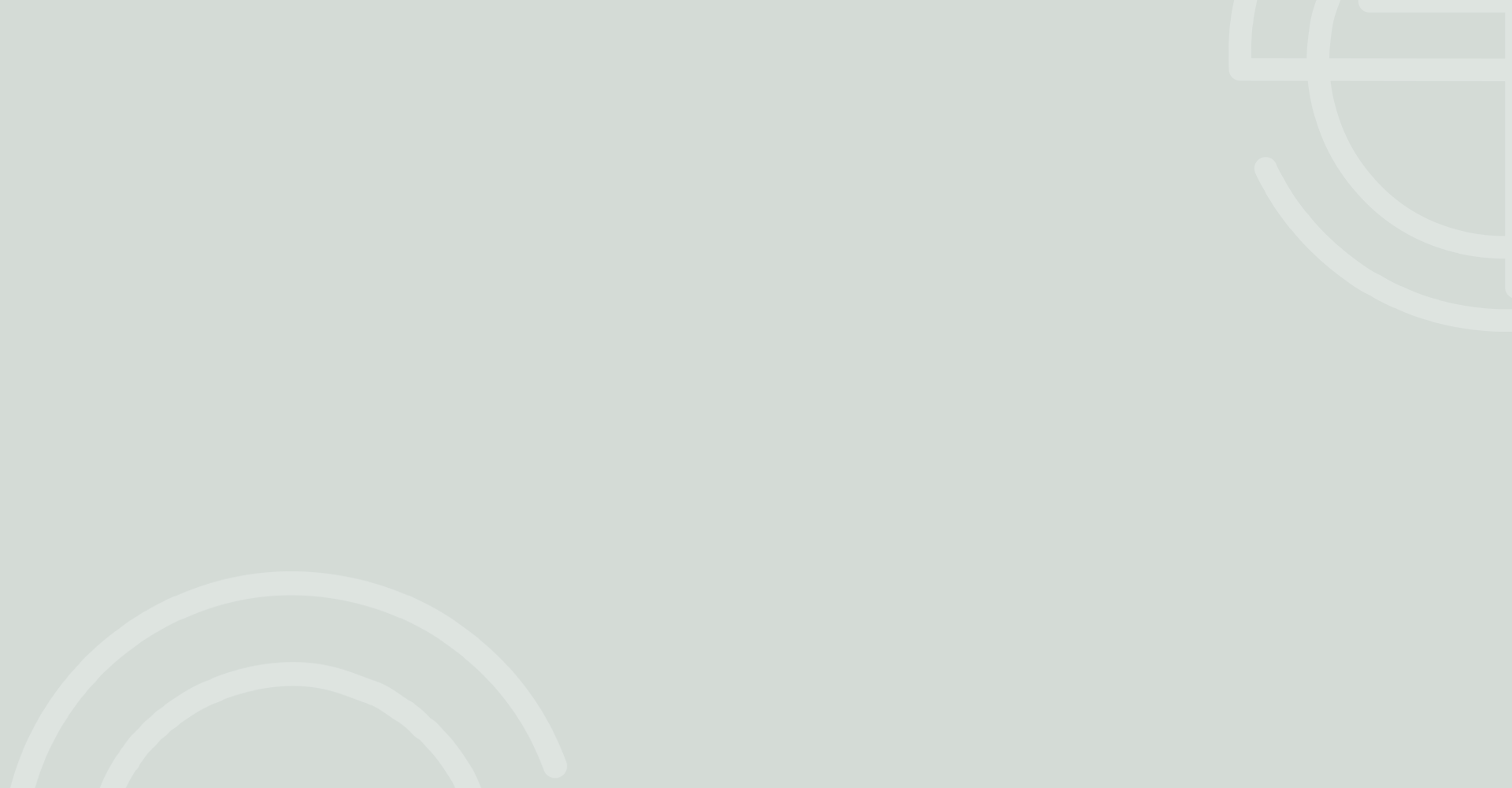